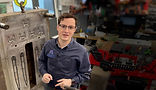
How to MOVE-A-MOLD from a current or past supplier to ASH


If your group has existing molds and you wish to benefit from ASH’s talents, you can move your molds with absolute assurance that your needs will be given priority. Based on the placement of a minimum parts order, the availability of material, and a Quality Criteria agreement, ASH will:
Evaluate molds for manufacturing suitability (test one)
Source material and availability ideal for your components (test two)
Pending passing the first two tests, begin production within one week.
Produce components of equal or better than "last run" quality standards
Document, disassemble, and clean the molds while replacing wear items and evaluating long term mold capability
Inventory parts placed for blanket orders.
When transferring an injection mold to any new supplier, there are several steps to ensure a smooth transition and continued successful production of your parts.
Here's what anyone will likely need to do with your mold:
Initial Mold Evaluation:
-
Visual Inspection: The new supplier will thoroughly inspect the mold for any signs of damage, wear, or corrosion. This might involve checking for cracks, rust, or imperfections on the mold surfaces, gates, runners, and ejector pins.
-
Mold Documentation Review: If possible, provide all available documentation related to the mold, including:
-
Mold design drawings (CAD files)
-
Material specifications for mold components (steel type, cavity materials)
-
Processing parameters used by the previous molder (injection pressures, temperatures, cycle times)
-
Preventive maintenance records
-
-
Mold Qualification Process: The new supplier might conduct their own mold qualification process to verify the mold's functionality and performance in their specific machines. This may involve trial runs to assess factors like:
Required tonnage, support equipment, and special requirements.
Cycle time repeatability
Part quality and dimensional accuracy
Mold Modifications if Necessary:
-
Machine Compatibility: In some cases, minor modifications might be required to ensure the mold fits correctly on the new supplier's injection molding machines. This could involve adjustments to mounting points or sprue bushing compatibility.
-
Process Optimization: Based on the qualification runs and their experience, the new supplier might suggest adjustments to the processing parameters (pressure, temperature, etc.) to optimize the molding process for their specific equipment and achieve the desired part quality.
-
Mold Maintenance: Routine maintenance is crucial for mold longevity. The new supplier might recommend or perform some initial maintenance tasks based on their inspection and qualification process. This could include cleaning, lubrication, or minor repairs.
Communication & collaboration:
-
Open communication between you and the new supplier is essential throughout the process. Discuss your expectations for part quality, production timelines, and any specific requirements you have.
-
Collaboration is key. By sharing your experience with the previous molder and any challenges encountered, you can help the new supplier establish a successful molding process for your parts.
ADDITIONAL TIPS:
-
Maintain a safety stock of parts: Having a buffer of parts from the previous molder can help bridge any gaps in production while the new supplier gets up and running.
-
Consider a pilot run: If possible, negotiate a small pilot run with the new supplier to test the mold and finalize the process parameters before full-scale production.
-
Maintain good relationships: Even after transitioning to a new supplier, it's wise to maintain a positive relationship with the previous molder in case you need them in the future.
By following these steps and fostering open communication, you can ensure a smooth transition of your mold to the new supplier and minimize any disruption to your production schedule.
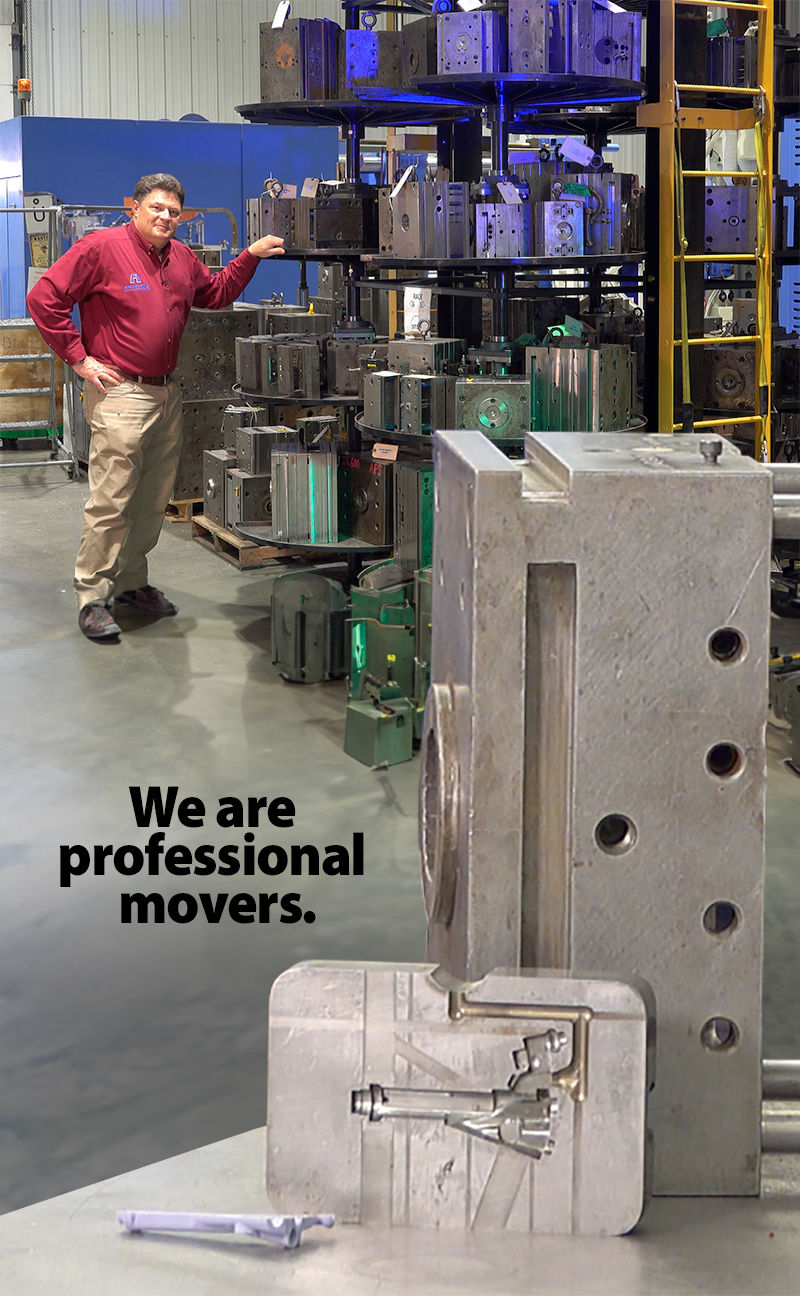

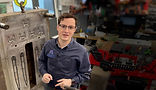
How to MOVE-A-MOLD™ from a current or past supplier to ASH

When transferring an injection mold to any new supplier, there are several steps to ensure a smooth transition and continued successful production of your parts.
Here's what anyone will likely need to do with your mold:
INITIAL MOLD EVALUATION:
-
Visual Inspection: The new supplier will thoroughly inspect the mold for any signs of damage, wear, or corrosion. This might involve checking for cracks, rust, or imperfections on the mold surfaces, gates, runners, and ejector pins.
-
Mold Documentation Review: If possible, provide all available documentation related to the mold, including:
-
Mold design drawings (CAD files)
-
Material specifications for mold components (steel type, cavity materials)
-
Processing parameters used by the previous molder (injection pressures, temperatures, cycle times)
-
Preventive maintenance records
-
-
Mold Qualification Process: The new supplier might conduct their own mold qualification process to verify the mold's functionality and performance in their specific machines. This may involve trial runs to assess factors like:
Required tonnage, support equipment, and special requirements.
Cycle time repeatability
Part quality and dimensional accuracy
MOLD MODIFICATIONS IF NECESSARY:
-
Machine Compatibility: In some cases, minor modifications might be required to ensure the mold fits correctly on the new supplier's injection molding machines. This could involve adjustments to mounting points or sprue bushing compatibility.
-
Process Optimization: Based on the qualification runs and their experience, the new supplier might suggest adjustments to the processing parameters (pressure, temperature, etc.) to optimize the molding process for their specific equipment and achieve the desired part quality.
-
Mold Maintenance: Routine maintenance is crucial for mold longevity. The new supplier might recommend or perform some initial maintenance tasks based on their inspection and qualification process. This could include cleaning, lubrication, or minor repairs.
COMMUNICATION & COLLABORATION:
-
Open communication between you and the new supplier is essential throughout the process. Discuss your expectations for part quality, production timelines, and any specific requirements you have.
-
Collaboration is key. By sharing your experience with the previous molder and any challenges encountered, you can help the new supplier establish a successful molding process for your parts.
ADDITIONAL TIPS:
-
Maintain a safety stock of parts: Having a buffer of parts from the previous molder can help bridge any gaps in production while the new supplier gets up and running.
-
Consider a pilot run: If possible, negotiate a small pilot run with the new supplier to test the mold and finalize the process parameters before full-scale production.
-
Maintain good relationships: Even after transitioning to a new supplier, it's wise to maintain a positive relationship with the previous molder in case you need them in the future.
By following these steps and fostering open communication, you can ensure a smooth transition of your mold to the new supplier and minimize any disruption to your production schedule.
If your group has existing molds and you wish to benefit from ASH’s talents, you can move your molds with absolute assurance that your needs will be given priority. Based on the placement of a minimum parts order, the availability of material, and a Quality Criteria agreement, ASH will:
Evaluate molds for manufacturing suitability (test one)
Source material and availability ideal for your components (test two)
Pending passing the first two tests, begin production within one week.
Produce components of equal or better than "last run" quality standards
Document, disassemble, and clean the molds while replacing wear items and evaluating long term mold capability
Inventory parts placed for blanket orders.
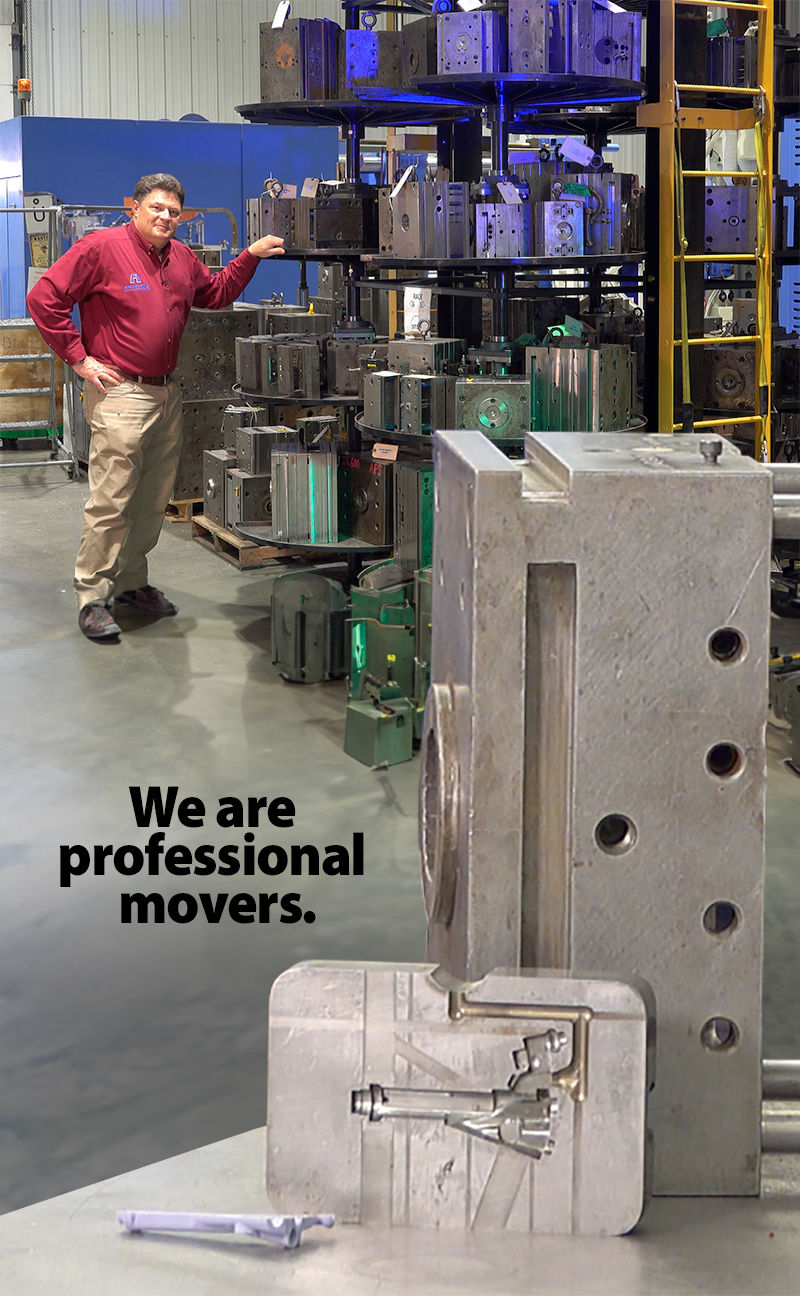
