
WHY SILICONE INJECTION MOLD?
LIQUID SILICONE RUBBER MOLDING offers HIGH VOLUME, INTRICATE PARTS WITH REPEATABILITY
Liquid Injection Molding (LIM) and Liquid Silicone Rubber (LSR) are very closely related terms, but there's a subtle difference. Think of LIM as the method and LSR as a specific material suited for that method. LSR and LIM are used interchangeably when referring to injection molding with Liquid Silicone Rubber.
The biggest benefit of Liquid Silicone injection molding (LIM) at ASH INDUSTRIES is unmatched stretchability and biocompatibility, making it ideal for demanding applications in the medical and consumer product fields.
Imagine creating medical components that move with the body or innovative baby products that are both gentle and durable. LSR molding also boasts exceptional precision and detail, allowing for intricate designs with a smooth, high-quality finish. Additionally, LSR offers fast cure times and the ability to create parts with superior strength and tear resistance.
Exceptional SILICONE parts come from smarter thinking.

Once cured, a thermoset permanently sets into its final shape and cannot be melted or remolded which makes it very resistant to heat and chemicals.

MEDICAL MOLDING
When it comes to medical-grade silicone parts, cleanliness is paramount.
ASH offers unparalleled medical molding capabilities with our state-of-the-art, ISO Class 7 clean room facility. This controlled environment minimizes airborne particles and contaminants, ensuring your medical components are manufactured to the strictest standards. This meticulous approach safeguards the integrity of your parts, fostering patient safety and regulatory compliance.
Trust us to deliver medical-grade SILICONE parts with unmatched quality and precision.

watch these videos
OVER MOLDING
Push the boundaries of metal parts with our innovative over molding process. Silicone rubber is overmolded onto plastics to absorb shock, act as a seal, give a soft feel to touch or to separate the non-biocompatible internal components of a device with a bioinert silicone elastomer.
This advanced technique utilizes an injection molded substrate and combines it with a second over-molded material, often a soft, rubber-like TPE, TPU, flexible PVC, or silicone material. This creates a single part with a unique blend of properties. Imagine ergonomic grips for enhanced user comfort, decorative finishes for a touch of style, or even improved functionality like water resistance.
Over molding opens a world of possibilities, allowing you to tailor your parts for superior performance, ergonomics and aesthetics.
MEDICAL
Overmolding Improves grip and control for surgical instruments like scalpels, forceps, and other instruments. Overmolding also works on hand held devices like nebulizers or blood pressure monitors. If you need enhanced durability and protection for delicate internal components of medical devices like defibrillators or anesthesia machines from impact and external factors. Luer fittings and other connectors benefit from overmolds that create secure seals to prevent leaks of fluids or gases.
Biocompatibility is improved with overmolding for implants that integrate with the body.

1
STARTING RIGHT!
DESIGN for MANUFACTURING
Optimizing Your Silicone Parts Digitally
Design for Manufacturability (DFM) is your secret weapon for transforming innovative concepts into production-ready injection molded parts. By collaborating with our DFM experts early on, you can identify potential roadblocks like complex geometries or uneven wall thickness. We'll suggest adjustments that optimize your design for efficient molding, minimizing waste and production costs. This ensures your parts are not only functional but also manufacturable, saving you time and money while bringing your vision to life.
-
Reduced Production Costs: Streamlined designs minimize material waste, optimize cycle times, and simplify the molding process, leading to lower production costs.
-
Enhanced Quality: DFM helps avoid common molding defects like sink marks, warping, or short shots, ensuring your parts meet the highest quality standards.
-
Faster Time to Market: By identifying potential issues upfront, DFM allows for a smoother transition from design to production, accelerating your time to market.
People also ask:
LIM (Liquid Injection Molding) is like a toolbox, able to handle various liquid materials. LSR (Liquid Silicone Rubber) is a specific, high-performance material that fits perfectly in that toolbox. Both terms can be used interchangeably when referring to molding LSR, but LIM can also work with other liquid polymers like epoxies.
HCR (High Consistency Rubber) and LSR (Liquid Silicone Rubber) are both silicone rubber used in injection molding, but differ in flow and processing. HCR is a pre-mixed, gum-like material requiring heat curing, while LSR comes in two liquid parts and cures quickly at lower temperatures. ASH Industries does not manufacture HCR parts.
Choosing between TPE and LSR depends on your project's priorities. TPE, a reusable thermoplastic, is easier to work with and cost-effective for simpler parts. It offers design flexibility and comes in a wide range of colors. However, LSR, a thermoset silicone rubber, boasts superior heat resistance, elasticity, and biocompatibility, making it ideal for demanding applications or medical parts.
Silicone rubber boasts impressive elongation properties, typically stretching between 100% and 1100% of its original length before breaking. This exceptional elasticity makes it ideal for applications requiring flexibility and a wide range of motion.
Silicone injection molds last from hundreds of thousands of cycles to over a million. A silicone mold lifespan is extended thanks to our maintenance, structure, SPI classification, and materials.
While silicone rubber is known for its elasticity, its tensile strength, which measures force before breaking, falls on a spectrum. It typically ranges from a modest 200 to 1,500 psi (pounds per square inch) depending on the specific type and formulation of the silicone.
After reinforced with silica fillers, the obtained light curing system can endow the light curing silicone elastomer with better mechanical properties under the condition of a lower viscosity of the precursor, the tensile strength and elongation at break can reach 525.5 kPa and 601%, respectively.
Thermosets strengthen when cured but form chemical bonds that make them impossible to remold. Thermoplastics do not form any chemical bond when curing, making them re-moldable and recyclable. This three-dimensional bonding in thermosets makes them stronger and more heat resistant than thermoplastics.


WHERE TO BUILD THE MOLD?
YOUR MOLD & IN-HOUSE TOOLROOM
2
THE MOST IMPORTANT PART OF THE PROCESS
In-house mold building is a game-changer for injection molding. Imagine seamless communication between design and toolmakers, speeding up development and getting your product to market faster. Direct control over quality ensures molds meet your exact specs, reducing defects. In-house tooling keeps everything streamlined, potentially saving costs. It's a strategic advantage for any serious molding company.


Here are some key factors in choosing a silicone molding supplier:
Expertise and Capabilities:
-
Experience: Look for a supplier with a proven track record in manufacturing silicone parts, particularly those similar to yours in complexity and application.
-
Material Options: Ensure they offer the specific silicone type (e.g., LSR, HCR) and durometer (hardness) you require for your part.
-
Part Complexity: Match your part's intricacies with the supplier's capabilities. Some specialize in highly detailed shapes, while others excel in simpler geometries.
-
Production Volume: Select a supplier with the capacity to handle your desired production volume efficiently.
-
Over molding: If you plan on incorporating overmolding with other materials, choose a supplier with experience in this technique.
Quality and Cost:
-
Quality Control: Inquire about their quality control procedures to ensure they meet your standards for dimensional accuracy, surface finish, and defect rates.
-
Cost Transparency: Get clear quotes outlining upfront costs like tooling, material fees, and per-unit part costs. Consider hidden fees or potential cost variations.
Additional Considerations:
-
Communication and Customer Service: Choose a supplier with good communication practices and a willingness to collaborate throughout the design and production process.
-
Lead Times: Understand the supplier's lead times for mold creation and production runs to meet your project timeline.
-
Sustainability: If environmental responsibility is important to you, inquire about the supplier's sustainability practices in terms of material sourcing and waste management.
By carefully evaluating these factors, you can find a custom silicone parts supplier who aligns with your project requirements, delivers high-quality products, and provides a smooth and efficient partnership.

We are ENGINEERS and SILICONE Injection Molding Experts
Choosing the right silicone molding company for your custom SILICONE parts is crucial for success.
Liquid Injection Molding (LIM) and Liquid Silicone Rubber (LSR) are very closely related terms, but there's a subtle difference. Think of LIM as the method and LSR as a specific material suited for that method. LSR and LIM are used interchangeably when referring to injection molding with Liquid Silicone Rubber.
The biggest benefit of Liquid injection molding (LIM) at ASH INDUSTRIES is unmatched stretchability and biocompatibility, making it ideal for demanding applications in the medical and consumer product fields.
Imagine creating medical components that move with the body or innovative baby products that are both gentle and durable. LSR molding also boasts exceptional precision and detail, allowing for intricate designs with a smooth, high-quality finish. Additionally, LSR offers fast cure times and the ability to create parts with superior strength and tear resistance.
Exceptional SILICONE parts come from smarter thinking.

Once cured, a thermoset permanently sets into its final shape and cannot be melted or remolded which makes it very resistant to heat and chemicals.

When it comes to medical-grade silicone parts, cleanliness is paramount.
ASH offers unparalleled medical molding capabilities with our state-of-the-art, ISO Class 7 clean room facility.
MEDICAL MOLDING

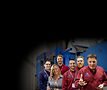
GET THE BALL ROLLING
Maybe you don't know which process to use, so let us help with a free engineering consult.
This is where you get great ideas
The earlier you get your supplier involved, the better chance that you will save something big. It could be time, money, functionality or even a new idea.
We specialize in the "tough challenges", the projects that need extra attention, experimentation or a new material. There's no better molding company than ASH to do this.

GET THE BALL ROLLING
Maybe you don't know which process to use, so let us help with a free engineering consult.
This is where you get great ideas
The earlier you get your supplier involved, the better chance that you will save something big. It could be time, money, functionality or even a new idea.
We specialize in the "tough challenges", the projects that need extra attention, experimentation or a new material. There's no better molding company than ASH to do this.
ASH FACTS:
-
Thermoplastic Injection Molding
-
Rotomolding
-
Tool & Die manufacturing
-
Silicone Molding
-
3D Printing Production
-
Design for Manufacturing (DFM)
-
Low volume 3D production
-
3D Plastic Printing
-
Metal Injection Molding
-
Yes, ASH can help you manufacture your parts in low volume. We can even 3D print your first prototypes. When you want to have less than 1000 but don't want to pay for full production runs we have a flat rate low volume program called SUPERMOLD. This can have many benefits, including a faster time to market and a low initial investment but still allow you to produce high-quality parts.
Of course NDA's are necessary to protect your IP. We value privacy and confidentiality and that is one of your main reasons for making parts in the USA. NDA's are enforceable here unlike sourcing overseas. Confidentiality is one of the most important factors in choosing a new molding supplier.
We are ISO 9001 compliant and ISO 13485 with a ISO Class 7 medical cleanroom.
Yes we do, besides our founder graduating from Massachusetts Institute of Technology with a degree in 6-1, Electrical Engineering-Hardware, we also have a biomedical engineer, mechanical engineers and other manufacturing engineers on staff to help you think smarter to save money.

watch these videos
OVERMOLDING
Push the boundaries of plastic parts with our innovative overmolding process.
This advanced technique takes your injection molded base and seamlessly combines it with a second material, often a soft, rubber-like TPE. This creates a single part with a unique blend of properties. Imagine ergonomic grips for enhanced user comfort, decorative finishes for a touch of style, or even improved functionality like water resistance.
Overmolding opens a world of possibilities, allowing you to tailor your parts for superior performance, ergonomics and aesthetics.
FIREARMS
We understand the demands of firearm components. At ASH INDUSTRIES, we utilize high-precision injection molding to deliver parts known for their strength, reliability, and dimensional accuracy. Our commitment to quality ensures each component performs flawlessly, meeting the expectations of both manufacturers and firearms enthusiasts.
MEDICAL DEVICES
Overmolding Improves grip and control for surgical instruments like scalpels, forceps, and other instruments. Overmolding also works on hand held devices like nebulizers or blood pressure monitors. If you need enhanced durability and protection for delicate internal components of medical devices like defibrillators or anesthesia machines from impact and external factors. Luer fittings and other connectors benefit from overmolds that create secure seals to prevent leaks of fluids or gases.
Biocompatibility is improved with overmolding for implants that integrate with the body.
watch these videos
OVER MOLDING
Push the boundaries of metal parts with our innovative over molding process. Silicone rubber is overmolded onto plastics to absorb shock, act as a seal, give a soft feel to touch or to separate the non-biocompatible internal components of a device with a bioinert silicone elastomer.
This advanced technique utilizes an injection molded substrate and combines it with a second over-molded material, often a soft, rubber-like TPE, TPU, flexible PVC, or silicone material. This creates a single part with a unique blend of properties. Imagine ergonomic grips for enhanced user comfort, decorative finishes for a touch of style, or even improved functionality like water resistance.
Over molding opens a world of possibilities, allowing you to tailor your parts for superior performance, ergonomics and aesthetics.
MEDICAL
Overmolding Improves grip and control for surgical instruments like scalpels, forceps, and other instruments. Overmolding also works on hand held devices like nebulizers or blood pressure monitors. If you need enhanced durability and protection for delicate internal components of medical devices like defibrillators or anesthesia machines from impact and external factors. Luer fittings and other connectors benefit from overmolds that create secure seals to prevent leaks of fluids or gases.
Biocompatibility is improved with overmolding for implants that integrate with the body.