

WHY ROTATIONAL MOLD?
ROTATIONAL MOLDING MAKES LARGE HOLLOW PARTS WITH CONSISTENT WALL THICKNESS

Rotational molding offers a unique phenomenon called "self-skinning." During the molding process, the plastic closest to the mold cavity cools and solidifies first. This creates a denser outer "skin" with a smoother finish, while the inner layer cools and solidifies later. This self-skinning effect provides a combination of a strong, protective outer layer and a lighter, more insulated interior in the final product.
Rotational molding offers a winning combination of efficiency and versatility. Its hollow one-piece forming allows for complex shapes, consistent wall thickness, and even integrated hinges – all in a single molding cycle.
This cost-effective process is ideal for creating durable, long-lasting parts for everything from toys and coolers to industrial tanks and kayaks.
Do you need tough, durable plastic parts that are anything but ordinary? Look no further than ASH INDUSTRIES, your one-stop shop for custom rotational molding solutions!
Rotomolding creates three-dimensional hollow shapes in a single cycle. Perfect for complex designs with integrated features like hinges and compartments. Offers consistent wall thickness throughout, leading to superior strength and durability.
Contact us today and let's roto-mold your next success story!
Our ASH™ rotational molding offers almost endless potential as far as design capabilities are concerned. For instance, the process can maintain uniform wall thicknesses better than other plastic parts. It also thrives at producing parts with double wall thicknesses and is ideal for molding thicker corners. Wall thicknesses and part weight can also be easily controlled via the process.
Rotational molding offers a winning combination of efficiency and versatility. Its hollow one-piece forming allows for complex shapes, consistent wall thickness, and even integrated hinges – all in a single molding cycle.
This cost-effective process is ideal for creating durable, long-lasting parts for everything from toys and coolers to industrial tanks and kayaks.
Do you need tough, durable plastic parts that are anything but ordinary? Look no further than ASH INDUSTRIES, your one-stop shop for custom rotational molding solutions!
Rotomolding creates three-dimensional hollow shapes in a single cycle. Perfect for complex designs with integrated features like hinges and compartments. Offers consistent wall thickness throughout, leading to superior strength and durability.
Contact us today and let's roto-mold your next success story!

Rotational molding offers a unique phenomenon called "self-skinning." During the molding process, the plastic closest to the mold cavity cools and solidifies first. This creates a denser outer "skin" with a smoother finish, while the inner layer cools and solidifies later. This self-skinning effect provides a combination of a strong, protective outer layer and a lighter, more insulated interior in the final product.
ADVANTAGE OF FOAM-FILLED HOLLOW PARTS
There are several advantages to adding foam to hollow rotational molded parts:
-
Increased Strength and Rigidity: Hollow parts can be susceptible to bending or warping under pressure. Filling them with foam creates a strong core, significantly improving the structural integrity of the part. This can possibly allow for thinner walls to be used while maintaining overall strength, which can also save on material costs.
-
Foam is inherently buoyant, making it ideal for applications where the part needs to float. Filling a hollow kayak or cooler with foam ensures it stays afloat even when loaded with gear.
-
Enhanced Insulation: Foam acts as a good insulator, helping to regulate temperature within the part. This can be beneficial for coolers keeping contents cold, or for hot water tanks minimizing heat loss.
-
Vibration Damping: The foam core can absorb vibrations and dampen noise, making the final product quieter and reducing wear on components. This is valuable for applications like machinery housings or transportation cases.


VIDEO SPED UP 3X TO SHOW PROCESS
PLASTIC PARTS UP TO 12' LONG

1
STARTING RIGHT!
DESIGN for MANUFACTURING
Optimizing Your Plastic Parts Digitally
Design for Manufacturability (DFM) is your secret weapon for transforming innovative concepts into production-ready roto-molded parts. By collaborating with our DFM experts early on, you can identify potential manufacturing roadblocks. We'll point out potential design-driven challenges and suggest adjustments that optimize your design for efficient molding, minimizing waste and production costs. This ensures your functional parts are also manufacturable, saving you time and money while bringing your vision to life.
-
Reduced Production Costs: Streamlined designs minimize material waste, optimize cycle times, and simplify the molding process, leading to lower production costs.
-
Enhanced Quality: DFM helps identify potential design-driven molding defects like sink marks, warping, or hard to fill areas, ensuring your parts meet the highest quality standards.
-
Faster Time to Market: By identifying potential issues upfront, DFM allows for a smoother transition from design to production, accelerating your time to market.

MOLD CONTROL
WHY YOU NEED AN IN-HOUSE TOOLROOM
THE MOST IMPORTANT PART OF THE PROCESS
In-house mold building is a game-changer for injection molding. Imagine seamless communication between design and toolmakers, speeding up development and getting your product to market faster. Direct control over quality ensures molds meet your exact specs, reducing defects. In-house tooling keeps everything streamlined, potentially saving costs. It's a strategic advantage for any serious molding company.
2



GET THE BALL ROLLING
Maybe you don't know which process to use, so let us help with a free engineering consult.
This is where you get great ideas
The earlier you get your supplier involved, the better chance that you will save something big. It could be time, money, functionality or even a new idea.
We specialize in the "tough challenges", the projects that need extra attention, experimentation or a new material. There's no better molding company than ASH to do this.
People also ask:
Rotational molding, also called rotomolding, creates hollow plastic parts by heating and rotating a mold filled with powdered plastic. This technique excels at making large, one-piece items like kayaks and coolers, thanks to its ability to ensure even wall thickness throughout the part.
Rotational molding excels at one-piece hollow shapes with consistent wall thickness, ideal for large, robust parts. Injection molding, on the other hand, is better suited for intricate, high-precision parts with potentially varying wall thicknesses, often producting multiple parts per cycle that need assembly.
In the world of roto molding, linear low-density polyethylene (LLDPE) is a cost-effective material due to its versatility, processability, and durability.
Rotational molding excels for low to medium volumes, and mold creation costs are cost effective compared to injection molding or blow molding. Lower volume production runs in rotational molded parts will be more cost effective than in blow molding. In fact, because the material is often hand loaded, frequent color changes can be possible.
Because rotational molding is a low pressure process, molds may experience less wear and tear than other processes.
The process of rotomolding is an environmentally-friendly one. No chemicals or dangerous toxins are released during production. There is also less material wastage compared to manufacturing with other materials, like metal or concrete.
ASH FACTS:
-
Thermoplastic Injection Molding
-
Rotomolding
-
Tool & Die manufacturing
-
Silicone Molding
-
3D Printing Production
-
Design for Manufacturing (DFM)
-
Low volume 3D production
-
3D Plastic Printing
-
Metal Injection Molding
-
Yes, ASH can help you manufacture your parts in low volume. We can even 3D print your first prototypes. When you want to have less than 1000 but don't want to pay for full production runs we have a flat rate low volume program called SUPERMOLD. This can have many benefits, including a faster time to market and a low initial investment but still allow you to produce high-quality parts.
Of course NDA's are necessary to protect your IP. We value privacy and confidentiality and that is one of your main reasons for making parts in the USA. NDA's are enforceable here unlike sourcing overseas. Confidentiality is one of the most important factors in choosing a new molding supplier.
We are ISO 9001 compliant and ISO 13485 with a ISO Class 7 medical cleanroom.
Yes we do, besides our founder graduating from Massachusetts Institute of Technology with a degree in 6-1, Electrical Engineering-Hardware, we also have a biomedical engineer, mechanical engineers and other manufacturing engineers on staff to help you think smarter to save money.
Choosing the right company for your custom ROTATIONAL MOLDED parts is crucial for success.
Here are some key factors in choosing a roto molding supplier:
Expertise and Capabilities:
-
Experience: Look for a supplier with a proven track record in rotational molding, particularly for parts similar to yours in complexity and size.
-
Mold Design: Choose a supplier with experience in designing and building rotational molds to ensure optimal part quality and production efficiency.
-
Material Options: Ensure they have experience with the specific type of plastic material you require for your part (e.g., LLDPE, HDPE) and can offer color options if needed.
-
Part Complexity: Match your part's intricacies with the supplier's capabilities. Some specialize in highly complex shapes, while others excel in simpler geometries.
-
Secondary Services: Consider if you need additional services like finishing (e.g., painting, assembly) and inquire if the supplier offers them in-house or partners with reliable providers.
Quality and Cost:
-
Quality Control: Inquire about their quality control procedures to ensure they meet your standards for dimensional accuracy, surface finish, and part consistency.
-
Cost Transparency: Obtain clear quotes that detail upfront costs like mold design, mold creation, material costs, and per-unit part costs. Consider hidden fees or potential cost variations based on complexity.
Additional Considerations:
-
Communication and Customer Service: Choose a supplier with good communication practices and a willingness to collaborate throughout the design, prototyping, and production process.
-
Lead Times: Understand the supplier's lead times for mold creation and production runs to meet your project timeline.
-
Location and Certifications: Consider factors like geographical proximity for easier collaboration and any relevant industry certifications they hold.
-
Minimum Order Quantities (MOQs): Some suppliers have minimum order requirements. Ensure the supplier's MOQ aligns with your production needs, especially if you' re planning a smaller initial run.
By carefully evaluating these factors, you can find a rotational molding supplier who aligns with your project requirements, delivers high-quality parts efficiently, and provides clear communication and support throughout the process.

1
IT STARTS WITH DESIGN
DESIGN for MANUFACTURING
Optimizing Your Plastic Parts Digitally
Design for Manufacturability (DFM) is your secret weapon for transforming innovative concepts into production-ready roto-molded parts. By collaborating with our DFM experts early on, you can identify potential manufacturing roadblocks. We'll point out potential design-driven challenges and suggest adjustments that optimize your design for efficient molding, minimizing waste and production costs. This ensures your functional parts are also manufacturable, saving you time and money while bringing your vision to life.
-
Reduced Production Costs: Streamlined designs minimize material waste, optimize cycle times, and simplify the molding process, leading to lower production costs.
-
Enhanced Quality: DFM helps avoid common molding defects like sink marks, warping, or short shots, ensuring your parts meet the highest quality standards.
-
Faster Time to Market: By identifying potential issues upfront, DFM allows for a smoother transition from design to production, accelerating your time to market.

WHERE TO BUILD THE MOLD?
2

THE MOST IMPORTANT PART OF THE PROCESS
In-house mold building is a game-changer for injection molding. Imagine seamless communication between design and toolmakers, speeding up development and getting your product to market faster. Direct control over quality ensures molds meet your exact specs, reducing defects. In-house tooling keeps everything streamlined, potentially saving costs. It's a strategic advantage for any serious molding company.
YOUR MOLD & IN-HOUSE TOOLROOM
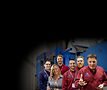
GET THE BALL ROLLING
Maybe you don't know which process to use, so let us help with a free engineering consult.
This is where you get great ideas
The earlier you get your supplier involved, the better chance that you will save something big. It could be time, money, functionality or even a new idea.
We specialize in the "tough challenges", the projects that need extra attention, experimentation or a new material. There's no better molding company than ASH to do this.
ADVANTAGE OF FOAM-FILLED HOLLOW PARTS
There are several advantages to adding foam to hollow rotational molded parts:
-
Increased Strength and Rigidity: Hollow parts can be susceptible to bending or warping under pressure. Filling them with foam creates a strong core, significantly improving the structural integrity of the part. This can possibly allow for thinner walls to be used while maintaining overall strength, which can also save on material costs.
-
Foam is inherently buoyant, making it ideal for applications where the part needs to float. Filling a hollow kayak or cooler with foam ensures it stays afloat even when loaded with gear.
-
Enhanced Insulation: Foam acts as a good insulator, helping to regulate temperature within the part. This can be beneficial for coolers keeping contents cold, or for hot water tanks minimizing heat loss.
-
Vibration Damping: The foam core can absorb vibrations and dampen noise, making the final product quieter and reducing wear on components. This is valuable for applications like machinery housings or transportation cases.

GET THE BALL ROLLING
Maybe you don't know which process to use, so let us help with a free engineering consult.
This is where you get great ideas
The earlier you get your supplier involved, the better chance that you will save something big. It could be time, money, functionality or even a new idea.
We specialize in the "tough challenges", the projects that need extra attention, experimentation or a new material. There's no better molding company than ASH to do this.
